Durable ceramic composites with superhard particles for wear-resistant cutting tools - DURACER
The DURACER project developed ceramic tool composites based on alumina (Al2O3) reinforced with super-hard cubic boron nitride (cBN) particles. The composites, in accordance with the project assumptions, were obtained using the Spark Plasma Sintering (SPS) method.
The main challenge was the metastability of cBN under SPS conditions. At high temperatures, cBN (like diamond) transforms into a hexagonal, graphite-like form (hBN) and therefore ultra-high pressure must also be ensured during its sintering to avoid cBN-->hBN transition. Therefore, cBN composites are usually obtained by expensive and complicated High Pressure – High Temperature (HPHT) methods at temperatures of 1900-2200 °C and pressures of 5.5-8 GPa.
Due to the low content of the superhard phase in the DURACER composites (up to 30% by volume) and the use of ultrafine powders characterized by a relatively low sintering temperature as the binding phase, the composites were obtained by the SPS method at pressures from 60 to 150 MPa (two orders of magnitude less than in HPHT). Optimization of the composition of the bonding phase ensured a low enough sintering temperature (1300- 1400 °C) to significantly reduce the formation of hBN and obtain composites with very good mechanical properties. Finally, a series of cutting inserts with RNGN (round) geometry was manufactured from selected, most promising composites. The inserts have been tested by means of dry turning of a variety of hardened steels (60-65 HRC) and Inconel Alloy 718 under various cutting conditions.
In the worst case, the lifetime of DURACER inserts when cutting hardened steel was comparable to pure Al2O3 inserts (popular cutting tool ceramics), but in the best case, the lifetime of DURACER tools was up to tens of times longer (90 min) than the reference Al2O3 insert (2 min). The lifetime of the DURACER inserts when cutting Inconel at high speed (250 m/min) was approximately 5 minutes, which is comparable to the lifetime of advanced ceramic inserts from leading tooling companies.
Tests have shown that DURACER tools are best suited for machining hardened steels, but can also be successfully used for Inconel. Potential consumers of the project results are mainly manufacturers of cutting tools and tools users but other applications of developed materials e.g. at extreme conditions (high mechanical loads, elevated temperatures, aggressive environments) are not excluded.
The dissemination activities resulting from the project can be summarized in numbers as follows: peer reviewed articles – 17, conference proceedings – 12, "Scientific nights" and "Open days" – 6. In order to protect the DURACER solution, a patent application was also filed.
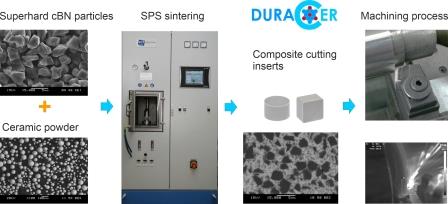